There is an interesting intersection at work between the disciplines of mechanical engineering and orthopedic surgery. For example, spine surgeon Dr. Michael Hisey of Texas Back Institute earned his undergraduate degree in mechanical engineering from The California Institute of Technology. Of course, he then went on to medical school and specialized in orthopedic surgery, but his fascination with engineering continues to this day. This partially explains his interest in the 3D printing of medical devices.
A Brief History of 3D Printing
While it seems that 3D technology has just recently burst on the scene, in fact, it has been around since 1981. It was originally known as “additive manufacturing” and was invented by Hideo Kodama of Nagoya Municipal Industrial Research Institute in Japan. The first medical application of 3D printing occurred in 1999 when scientists at Wake Forest Institute for Regenerative Medicine printed synthetic scaffolds of a human bladder and then coated them with the cells of human patients. The newly generated tissue was then implanted into the patients with little to no chance that their immune systems would reject them, as they were made of their own cells.
The market for 3D printing is growing rapidly. One example of this growth is Essentium Inc., a Texas-based 3D printing company that is transforming additive manufacturing for use in a broad range of industries.
3D Printing & Spine Surgery in Today’s Operating Room
This evolution of 3D printing has gotten the attention of engineer turned spine surgeon, Dr. Michael Hisey.
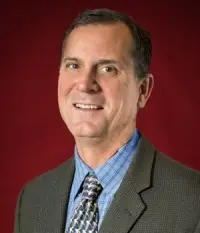
“While it might surprise some, 3D printing has been used in spine surgery for many years,” he said. “The first use of this process was in ‘rapid prototyping.’ When a surgeon or company would design an implant, they wanted to ensure that it would work. They would therefore build the prototype of a new implant out of plastic. Ultimately, it would be made of metal, but they wanted to make sure it fit and worked with other parts of the spine. Early on, these plastic implants were not used in patients. They were used as a kind of ‘trial balloon’ to see if the process was viable.”
Dr. Hisey notes that the 3D printing process can now use metal, rather than plastic. When it became possible to print a metal such as titanium, printers could build implants with geometries that weren’t even possible before with either molds or machining. This allowed implants to be made with porosity (i.e. with holes in their surface) that could never be created by standard manufacturing. This porosity allows for better tissue integration and, often, quicker healing.
One of the primary advantages of 3D printing in spine surgery is its capability to precisely reproduce a model of the bones and joints of the spine. This process is dependent on having precise measurements of the bone. Dr. Hisey notes that for many years CT scans have been able to produce extremely accurate measurements of bones and joints. Using the CT scans, the surgeon can produce a plastic recreation of the patient’s spine which allows the surgeon to better plan the operation.
“This allows us to observe the spine in three dimensions, hold it in our hands, and to get an accurate look at the patient’s spinal anatomy,” he said. “Essentially, we can off-load the data from the CT scan and then replicate the bony structure with excellent precision and in three dimensions.
“There are also measuring tools in the software of the CT scans. This allows the surgeon to accurately predict such factors as the size of the screws and what size implants will be needed to stabilize the bone. Again, this technology is already being used and it allows for more efficiency in ordering implants for a patient, thereby reducing the cost of the procedure to patients and their insurers.”
Back to the Future of Biomedical 3D Printing
Once technology begins to take hold in an industry, it typically expands exponentially. The immediate future of 3D looks bright.
Dr. Hisey explains that in addition to the customized implants that are now being used, there will soon be “off-the-shelf” implants that allow for a greater surface area on which bone can grow, and better porosity that will help speed the recovery of implant surgery.
“We’re getting to the point where we can build implants that might have flexibility characteristics that better match the body’s structure,” he said. “We do this by putting in ‘struts’ that allow the implant to flex, more than a solid piece of metal might. This allows the implant to better work with the patient’s bones and not collapse existing bone.
“I can also see the possibility of 3D printing a flexible disc in the near future that would be used for replacement of damaged or diseased discs.”
According to Dr. Hisey, “We ain’t seen nothing yet!”
“In the next 20 years, I would expect that we would have a 3D printer that lives in the hospital,” he said. “This would allow us to plan the surgery the day before and then have the implant made as we are preparing the patient for surgery. It comes out of the printer sterilized and ready to be used for the patient. And for trauma surgery, a patient brought into emergency needing an implant could be treated in minutes.
“In addition, we would also have the ability to reproduce surgical equipment or be able to reproduce broken instruments in minutes. Sometimes instruments are damaged during the procedure. If a surgical hammer is broken during the operation, a 3D printer could produce another one, an exact replica, in minutes. This reduces the number of instruments that are stored, saving money for the patient, hospital and insurance carrier.
“Using this ‘just-in-time inventory’ or ‘as you need it’ strategy will mean no more deliveries will be needed. This will save time and, of course, reduce the cost of the procedure.”
Improving Patient Outcomes Through 3D Technology
The ability to 3D print metal such as titanium is advancing rapidly. This process can enable better load-sharing than that of machined implants. Since most of the implants in spine surgery are metal and this technology will only get better and better, patient outcomes – during the procedure and recovery – will constantly improve.
“Our accuracy is improving,” Dr. Hisey said. “Imaging has never been better and with the increase in computational power, it will only continue to increase. And the materials we can print are evolving. 3D printing will ultimately allow us to customize implants and better match a patient’s anatomy which we expect to lead to quicker recovery, more accurate correction of deformities and better relief of symptoms. The combination of engineering, technology and medicine should produce better results than were previously possible. This is truly an exciting time for surgeons and patients.”
The most exciting aspects of medical 3D printing are the potential it has to improve patient outcomes while reducing the of the costs of procedures. While the technology is still in its nascent stages, as more printers are developed and produced, their accuracy will improve and availability will expand. This is a big win for everyone involved.